1. Introduction: The Rise of Smart Manufacturing
Smart Manufacturing: has undergone a profound transformation, driven by the integration of cutting-edge technologies that redefine efficiency, precision, and sustainability. From the assembly lines of the Industrial Revolution to the interconnected systems of today, the evolution of Smart Manufacturing Innovations reflects humanity’s relentless pursuit of innovation and progress.
The emergence of Smart Manufacturing Innovations, powered by advancements such as automation, artificial intelligence (AI), and the Internet of Things (IoT), has unlocked new possibilities. Unlike traditional manufacturing, smart manufacturing leverages data-driven processes and real-time analytics to optimize operations, reduce waste, and enhance productivity.
Key innovations, such as robotics, augmented reality (AR) for workforce training, and predictive maintenance systems, are empowering industries to adapt swiftly to market demands while minimizing downtime. Furthermore, sustainable practices supported by smart manufacturing are addressing the environmental challenges of industrial production, paving the way for greener solutions.
Today, smart manufacturing is not just a competitive advantage—it’s a necessity. As industries embrace these advancements, they are not only transforming their production capabilities but also redefining the future of manufacturing itself. In this blog, we delve deeper into the smart manufacturing shaping this revolution and explore the lasting impact they hold for the industry and society.
2. Automation and Robotics in Manufacturing: Redefining Productivity and Efficiency

Automation and robotics have become the backbone of modern smart manufacturing, enabling industries to streamline production processes and achieve unparalleled levels of efficiency. By leveraging cutting-edge technology, manufacturers can meet growing demand, reduce costs, and maintain a competitive edge in the evolving global market.
Click Here: Industry 5.0 Unveiled: Embracing Tomorrow’s Technological Revolution
Precision and Consistency
- Robotics bring unmatched precision and consistency to manufacturing tasks, minimizing errors and ensuring high-quality output. Advanced robots are capable of performing repetitive tasks with accuracy, contributing to enhanced productivity and reducing waste.
Increased Throughput
- Automation systems are designed to operate continuously, enabling faster production cycles without fatigue or downtime. This increases throughput and helps manufacturers scale operations effectively while meeting tight deadlines.
Flexible Manufacturing Systems
- Advanced automation integrates flexibility into production lines, allowing manufacturers to adapt quickly to changes in product design or market demand. Robotic systems can be programmed to handle diverse tasks, fostering versatility in manufacturing processes.
Cost Optimization
- By reducing the reliance on manual labor for routine tasks, automation and robotics minimize operational costs. Additionally, automated systems reduce material waste through precision, resulting in further savings for manufacturers.
Enhanced Safety
- Robotics take on dangerous or labor-intensive tasks, ensuring the safety of human workers. Automated systems operate in hazardous environments, reducing risks and improving overall workplace conditions.
Real-Time Monitoring and Analytics
- Smart robotics and automation systems are integrated with IoT and AI technologies to provide real-time data monitoring and analytics. These insights allow manufacturers to optimize workflows, predict maintenance needs, and prevent costly downtime.
Improved Scalability
- Automation enables rapid scaling of production without compromising quality. Manufacturers can expand capacity effortlessly, responding effectively to increased market demand or seasonal spikes.
Innovation in Collaborative Robots (Cobots)
- Collaborative robots, or cobots, are designed to work alongside human workers, enhancing productivity while preserving the need for human expertise. Cobots bring the benefits of automation while ensuring a harmonious partnership between technology and people.
Automation and robotics are revolutionizing smart manufacturing by providing efficiency, scalability, and adaptability. As industries continue to embrace these advancements, they not only streamline production but also set new standards for safety, precision, and innovation. The integration of smart systems promises a brighter and more productive future for the manufacturing sector.
3. Artificial Intelligence (AI) for Predictive Analytics: Transforming Manufacturing Efficiency
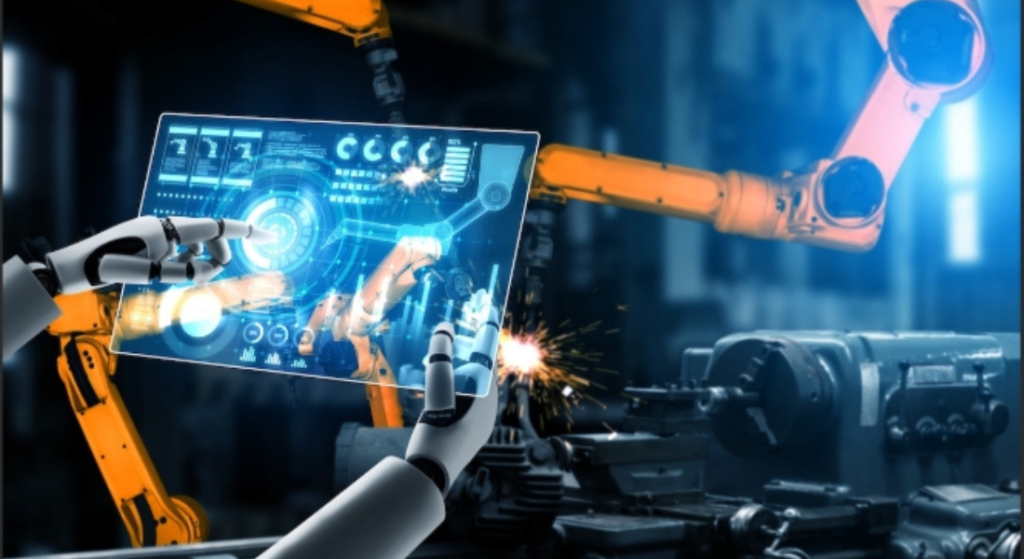
- Artificial Intelligence (AI) is revolutionizing predictive analytics in smart manufacturing, offering unparalleled precision in forecasting trends, optimizing workflows, and minimizing downtime. By leveraging powerful algorithms and real-time data, AI enables industries to anticipate challenges and make data-driven decisions that enhance efficiency and profitability.
Accurate Trend Forecasting
- AI excels in analyzing vast datasets to identify patterns and predict future trends. Manufacturers can anticipate market demands, optimize inventory, and align production schedules to meet customer needs efficiently. This predictive capability ensures better resource allocation and reduces the risk of overproduction or underproduction.
Optimizing Workflows Through Data Insights
- AI-driven systems provide actionable insights by analyzing real-time data from connected machines and sensors. This enables manufacturers to streamline workflows, identify bottlenecks, and enhance productivity. Smart automation guided by AI ensures that production processes operate at peak performance.
यह भी पढ़े: “5 Inspiring Features of Tata EV’s Future-Ready Design Revolutionizing Green Mobility”
Reducing Downtime with Predictive Maintenance
- AI-powered predictive maintenance systems monitor equipment health and detect anomalies before they lead to breakdowns. By analyzing sensor data, these systems predict when a machine is likely to fail, allowing for timely maintenance. This reduces unplanned downtime, extends equipment lifespan, and saves operational costs.
Supply Chain Optimization
- AI improves supply chain efficiency by predicting disruptions and suggesting alternative routes or suppliers. It ensures seamless coordination between production, inventory, and logistics, reducing delays and maintaining smooth operations.
Enhancing Decision-Making Through Machine Learning
- Machine learning models empower manufacturers to simulate various scenarios and evaluate the potential outcomes of different strategies. This enhances decision-making, enabling businesses to adapt swiftly to changing market dynamics and consumer behaviors.
Cost Reduction and Resource Efficiency
- AI optimizes resource utilization by reducing waste and ensuring efficient energy consumption. This not only lowers operational costs but also aligns with sustainability goals, benefiting both businesses and the environment.
Empowering Workforce with AI Insights
- By providing workers with real-time insights and intuitive dashboards, AI enables teams to make informed decisions quickly. This collaboration between human expertise and AI intelligence fosters innovation and efficiency.
AI for predictive analytics is transforming the manufacturing industry by ensuring proactive decision-making, reducing costs, and enhancing operational efficiency. As industries embrace this technological shift, they are poised to achieve higher productivity, improved competitiveness, and sustainable growth in a dynamic global market.
4. IoT Integration: Connecting Manufacturing Ecosystems for Smarter Operations
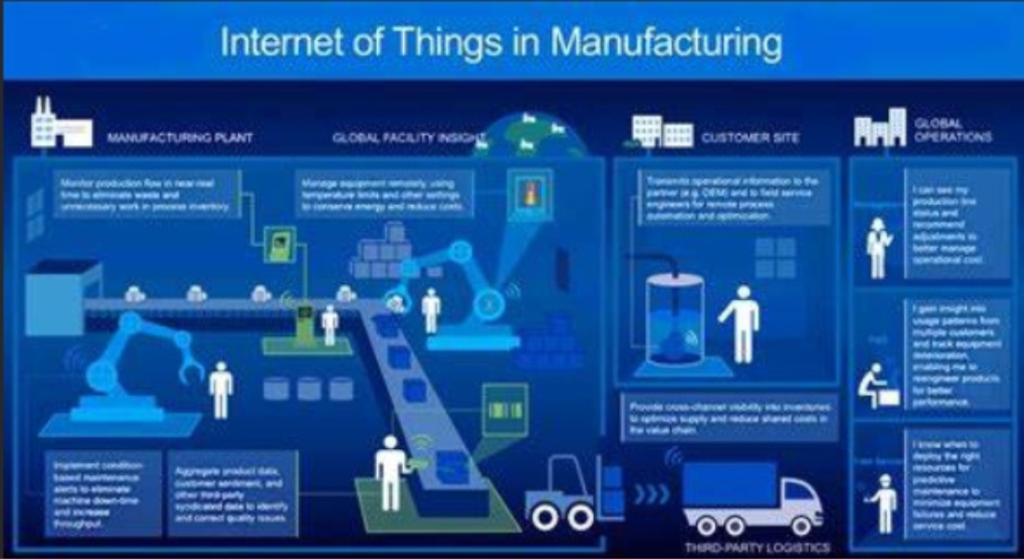
The Internet of Things (IoT) is transforming the manufacturing industry by creating connected ecosystems that enable smarter, more agile operations. By integrating IoT devices and technologies into manufacturing processes, industries can achieve unparalleled levels of efficiency, productivity, and adaptability in an increasingly competitive market.
Real-Time Monitoring for Enhanced Control
- IoT-enabled sensors and devices provide real-time data on machine performance, energy consumption, and production metrics. This transparency allows manufacturers to monitor operations with precision, identify inefficiencies, and make immediate adjustments for optimal output.
Seamless Connectivity Across Ecosystems
- IoT facilitates communication between machines, equipment, and systems, ensuring seamless integration across the manufacturing floor. This connectivity enables synchronized workflows, reducing bottlenecks and enhancing overall productivity.
Predictive Maintenance for Reduced Downtime
- IoT devices equipped with advanced analytics predict potential equipment failures before they occur. By scheduling maintenance proactively, manufacturers minimize unplanned downtime, extend the lifespan of machinery, and reduce repair costs.
Data-Driven Decision-Making
- IoT generates vast amounts of actionable data, empowering manufacturers to make informed decisions. This includes optimizing inventory management, forecasting demand, and improving supply chain coordination—all driven by real-time insights.
Improved Quality Assurance
- IoT enables automated quality checks throughout the production process. Sensors monitor variables like temperature, pressure, and moisture, ensuring consistent product quality and reducing wastage.
Agility in Adapting to Market Demands
- Connected IoT ecosystems allow manufacturers to respond quickly to changes in consumer preferences and market trends. Flexible production systems ensure manufacturers can pivot to new product designs or scale production based on demand.
Sustainability and Energy Efficiency
- IoT optimizes energy consumption by monitoring usage patterns and reducing waste. This aligns manufacturing operations with sustainability goals, making processes more environmentally friendly and cost-effective.
Enhanced Worker Safety
- IoT integrates wearable devices and safety systems to monitor worker health and environmental conditions. By detecting hazards in real-time, IoT ensures a safer workplace for employees.
IoT integration is revolutionizing manufacturing by creating interconnected ecosystems that drive efficiency, sustainability, and innovation. As industries continue to embrace IoT, they unlock the potential for smarter operations and gain a competitive edge in the dynamic global market.
5. Sustainable Manufacturing Practices: Pioneering a Greener Future
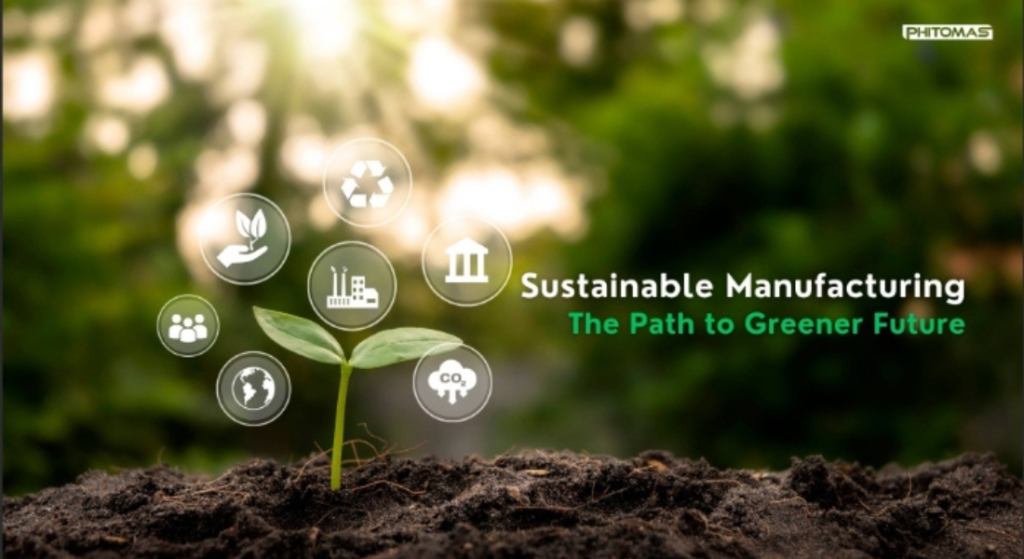
The manufacturing industry is embracing sustainability through eco-friendly innovations, with smart systems at the forefront of energy optimization and waste reduction. These practices not only address environmental concerns but also enhance operational efficiency and reduce costs, paving the way for a more sustainable future.
Energy Optimization with Smart Systems
- Modern manufacturing facilities use smart systems powered by IoT and AI to monitor energy consumption in real-time. By identifying usage patterns, these systems optimize energy usage, minimizing wastage. For instance, automated processes can power down idle machinery, reducing energy consumption without disrupting productivity.
Renewable Energy Integration
- Manufacturers are increasingly adopting renewable energy sources, such as solar panels, wind turbines, and geothermal systems, to power their facilities. Combined with energy storage solutions, these innovations reduce reliance on fossil fuels and significantly lower carbon emissions.
Waste Reduction Through Circular Manufacturing
- Circular manufacturing practices promote the reuse and recycling of materials, extending the lifecycle of resources. By repurposing waste products into raw materials, manufacturers minimize landfill contributions and create a closed-loop system that conserves resources.
Smart Waste Management
- Advanced analytics and IoT sensors are used to monitor waste generation and identify opportunities for reduction. For example, automated sorting systems can segregate recyclable and non-recyclable materials efficiently, streamlining waste disposal processes.
Eco-Friendly Packaging Solutions
- Manufacturers are turning to biodegradable and recyclable packaging materials. Additionally, optimized packaging designs reduce material usage and improve shipping efficiency, further cutting down on waste.
Water Conservation Technologies
- Smart water management systems in manufacturing plants monitor water usage and detect leaks, ensuring efficient consumption. Some facilities also recycle and treat wastewater for reuse, reducing water dependency and preserving natural resources.
Green Supply Chains
- Sustainable manufacturing extends beyond production to include eco-friendly logistics. Smart systems optimize transportation routes to reduce fuel consumption, while collaborations with green suppliers ensure that sustainability is upheld at every stage of the supply chain.
Carbon Neutral Commitments
- Many manufacturers are committing to carbon neutrality by adopting practices like carbon offsetting, using renewable materials, and investing in green technology innovations. These efforts align with global sustainability goals to mitigate climate change.
Sustainable manufacturing practices, driven by smart systems and innovative technologies, are revolutionizing the industry. By focusing on energy efficiency and waste reduction, manufacturers are building a greener future while staying competitive in the global market. These advancements not only benefit the environment but also resonate with consumers who value sustainability in the products they purchase.
6. Augmented Reality (AR) for Workforce Training and Maintenance: A Technological Revolution
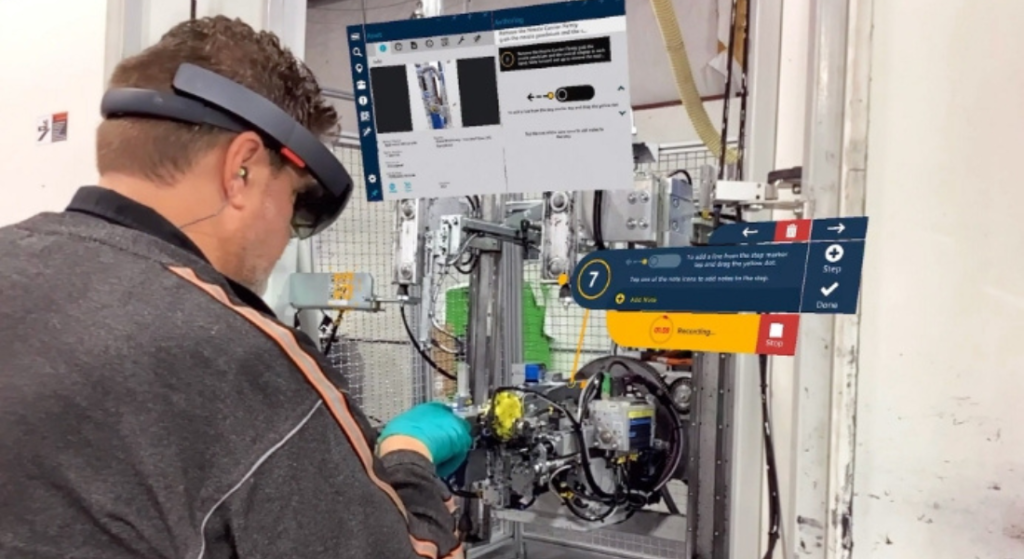
Augmented Reality (AR) is transforming how industries train employees and maintain equipment, offering immersive, interactive solutions that enhance learning and operational efficiency. By bridging the gap between the physical and digital worlds, AR is revolutionizing workforce development and equipment diagnostics with unparalleled precision and convenience.
Interactive and Immersive Training
- AR creates virtual training environments where employees can interact with lifelike 3D models and simulations. This hands-on experience allows trainees to practice complex tasks, such as assembling machinery or troubleshooting systems, without the risks associated with real-world scenarios.
On-The-Spot Guidance
- AR-powered devices provide real-time instructions overlaid on the physical environment, guiding workers step-by-step through processes. Whether it’s learning new equipment or performing routine tasks, AR ensures accuracy and reduces errors, even for inexperienced employees.
Equipment Diagnostics Made Simple
- AR simplifies equipment diagnostics by overlaying visual data onto machinery during inspections. Maintenance personnel can identify issues quickly by viewing operational details, fault indicators, and repair instructions in real time, streamlining the troubleshooting process.
Minimizing Downtime
- AR enables faster identification and resolution of equipment problems, minimizing downtime and maximizing productivity. Maintenance teams can access virtual manuals, collaborate remotely, and carry out repairs more efficiently, ensuring uninterrupted operations.
Remote Collaboration and Support
- AR facilitates remote collaboration, allowing experts to virtually assist workers on-site. Through AR-enabled devices, technicians can share visual instructions and annotations directly on the worker’s view, enhancing communication and reducing the need for travel.
Reducing Training Costs
- AR-based training eliminates the need for expensive physical prototypes and training materials. Virtual simulations provide scalable and cost-effective solutions, enabling companies to train larger groups without significant expenses.
Enhanced Worker Confidence and Competence
- By enabling experiential learning, AR boosts employee confidence and competence. Workers gain a better understanding of tasks and equipment, making them more capable of handling challenges and adapting to new technologies.
Sustainability in Training and Maintenance
- AR reduces the consumption of physical resources like paper manuals and training equipment, contributing to greener practices. This aligns manufacturing operations with sustainability goals while enhancing efficiency.
Augmented Reality is revolutionizing workforce training and equipment diagnostics, delivering interactive, cost-effective, and sustainable solutions that empower employees and optimize operations. As industries continue to adopt AR, they unlock new possibilities for innovation and productivity, setting the stage for a smarter, more connected future.
7. Future Trends in Smart Manufacturing: Embracing Emerging Technologies

Smart manufacturing is evolving rapidly, driven by groundbreaking technologies that promise to redefine efficiency, transparency, and connectivity. As industries adapt to the demands of a dynamic global market, emerging innovations like blockchain and 5G are paving the way for smarter, more agile operations.
Blockchain for Supply Chain Transparency
- Blockchain technology is revolutionizing supply chain management by creating tamper-proof records of transactions. This ensures transparency, traceability, and trust among stakeholders. Manufacturers can track the journey of raw materials and finished goods, ensuring compliance and reducing fraud2.
5G Connectivity for Lightning-Fast Operations
- The integration of 5G in manufacturing enables ultra-reliable, low-latency communication between devices. This technology supports real-time data exchange, enhances automation, and facilitates machine-to-machine communication, making operations faster and more efficient4.
Artificial Intelligence (AI) for Predictive Analytics
- AI continues to play a pivotal role in smart manufacturing by analyzing data to forecast trends, optimize workflows, and predict equipment maintenance needs. This reduces downtime and ensures seamless operations.
Internet of Things (IoT) for Connected Ecosystems
- IoT devices are transforming manufacturing floors into interconnected ecosystems. Sensors and smart devices provide real-time insights, enabling manufacturers to monitor operations, improve efficiency, and adapt swiftly to market demands.
Augmented Reality (AR) for Workforce Training
- AR is revolutionizing employee training by offering immersive simulations and real-time guidance. It also enhances equipment diagnostics, enabling faster troubleshooting and reducing downtime.
Sustainable Manufacturing Practices
- Emerging technologies are driving sustainability through energy optimization, waste reduction, and the use of eco-friendly materials. Smart systems ensure that manufacturing aligns with environmental goals.
Cybersecurity for Smart Factories
- As manufacturing becomes increasingly digital, robust cybersecurity measures are essential to protect sensitive data and ensure operational integrity. Technologies like blockchain and AI are enhancing security protocols.
These future trends in smart manufacturing are shaping a more connected, efficient, and sustainable industry. By embracing these innovations, manufacturers can stay ahead of the curve and unlock new possibilities for growth and competitiveness.